Integrated Production

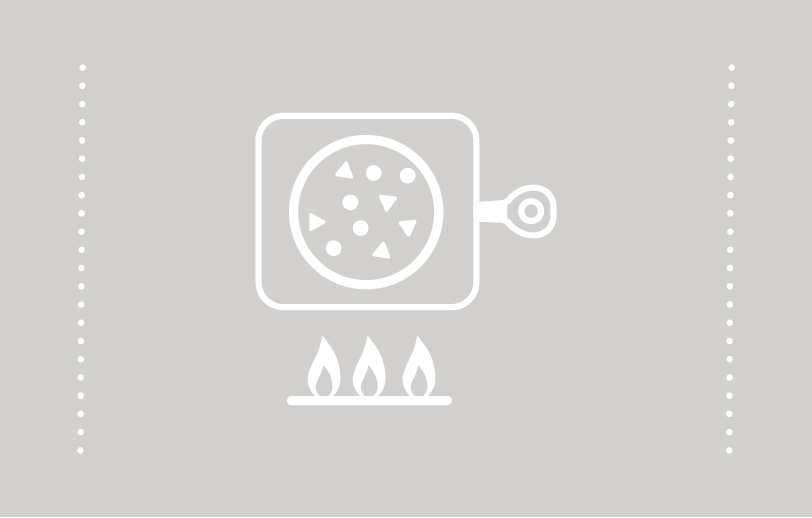
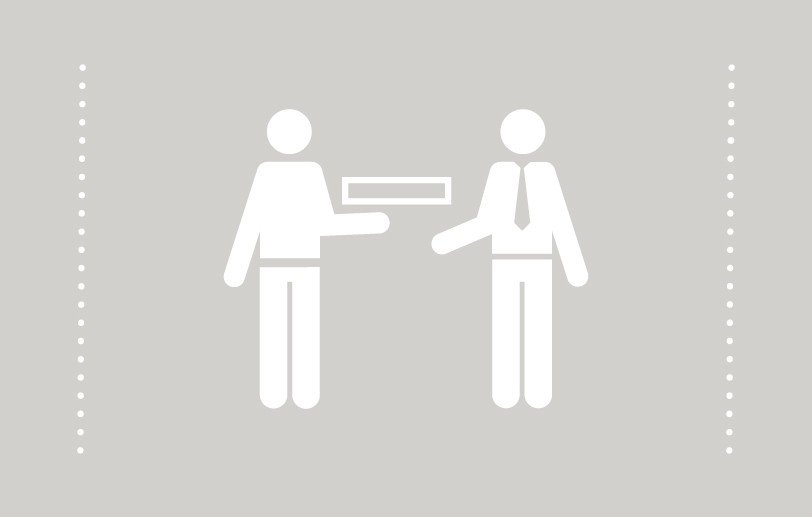
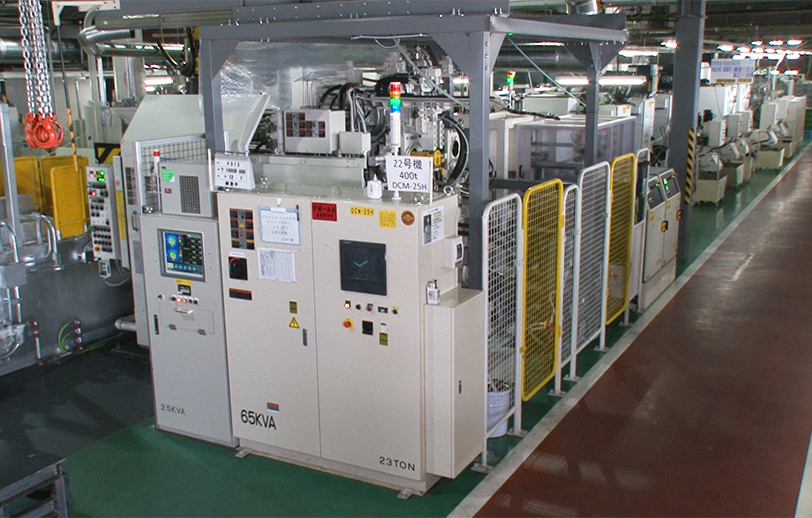
One-Piece Flow Line
The World’s First One-Piece Flow Line Accomplished by KSK
In our machining factory, the One-Piece Flow Line boasts a die-casting machine located at the head of the line, which enables 'one-piece flow' through the deburring, processing and inspection processes. This minimizes costs, space and stocks of unfinished parts. Toyota Motors presented us with its Technology Development Award in 2014. We currently have two such lines in operation, which have greatly improved the efficiency of valve body production. Just like in a pizzeria, the customer’s order is produced without any unnecessary stock or unfinished parts, and it is delivered within the lead time. In this sense, we have realized ‘pizza delivery shop' style manufacturing.
Newly-Developed
Ultra-Compact, Energy-Saving, High-Quality Die-casting Machine
IoT
On top: Casting Quality Monitoring System
Award Winning
Toyota's Technology & Development Award (in 2014)
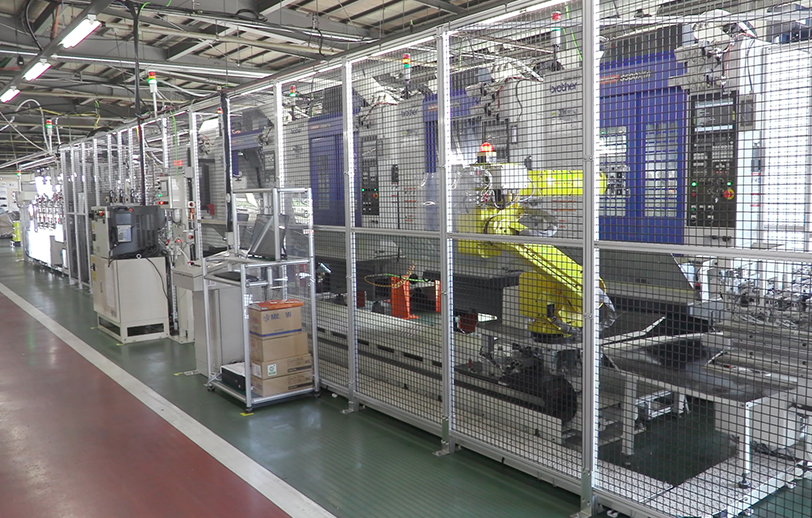
One-Piece Flow Line: Evolution
Complementing T5 Heat Treatment to the One-Piece Flow Line Concept
A CVT valve body is generally released from residual stress. For this reason, we have added a T5 heat treatment oven as an additional process to the new line for a new valve body order. Through optimized timing for the heat treatment and meticulously designed processes, we are able to reduce inventory of half-finished products to the minimum. While keeping to the One-Piece Flow Line concept, we have achieved a fully automated processing line.
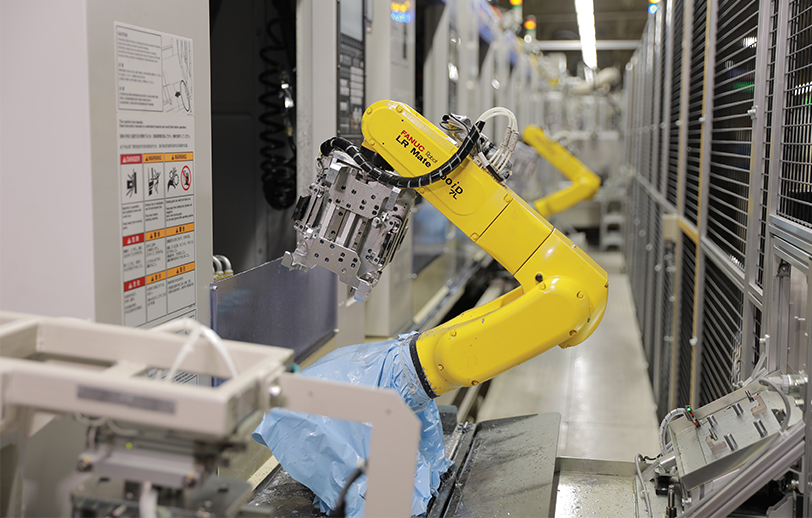
Unmanned Lines
Manufacturing Concept: Advancing IoT while Keeping the Focus on Each Single Part
The production conditions for each part are recorded in every process. The use of big data analysis will eventually lead to the elimination of defective parts. The manufacturing status of all parts in each process is monitored and documented in QR codes, from casting → deburring → T5 treatment → machining → inspection → shipping. This ensures traceability and that only 'good parts' are passed onto the next process. All handling is carried out by robots so that human operators can concentrate on the final inspection.
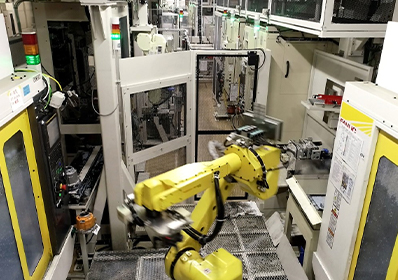
Robotic Mounting / Removal of Parts
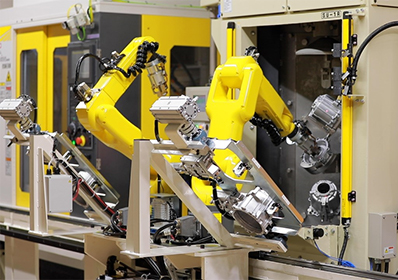
Automated Deburring of Cast Parts
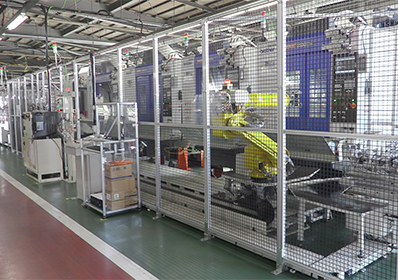
Transport by Mobile Robot
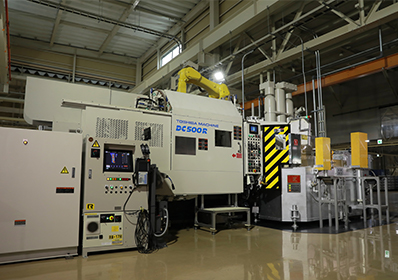
Unmanned Casting Line